Understanding Loose Nails and Their Importance
Loose nails are fundamental components in various industries, from construction to manufacturing. While they may seem like simple items, the production process is intricate, requiring precision and quality control to ensure their durability and efficiency. In this article, we will explore the key stages involved in producing high-quality loose nails, from raw material selection to final inspection.
MỤC LỤC BÀI VIẾT
1. Raw Material Selection
The first stage in producing loose nails is selecting the appropriate raw materials. Steel is the most common material used due to its strength and flexibility. The grade and quality of steel directly impact the final product’s performance. Producers often use low-carbon steel for its malleability, while high-carbon steel is preferred for its hardness and durability in demanding environments. Recycling scrap steel is also common, aligning with sustainable production practices.
Choosing the right material is crucial for ensuring the loose nail’s resilience and resistance to bending or corrosion. Manufacturers often work closely with suppliers to source high-quality steel that meets industry standards, which is the foundation for a successful production process.
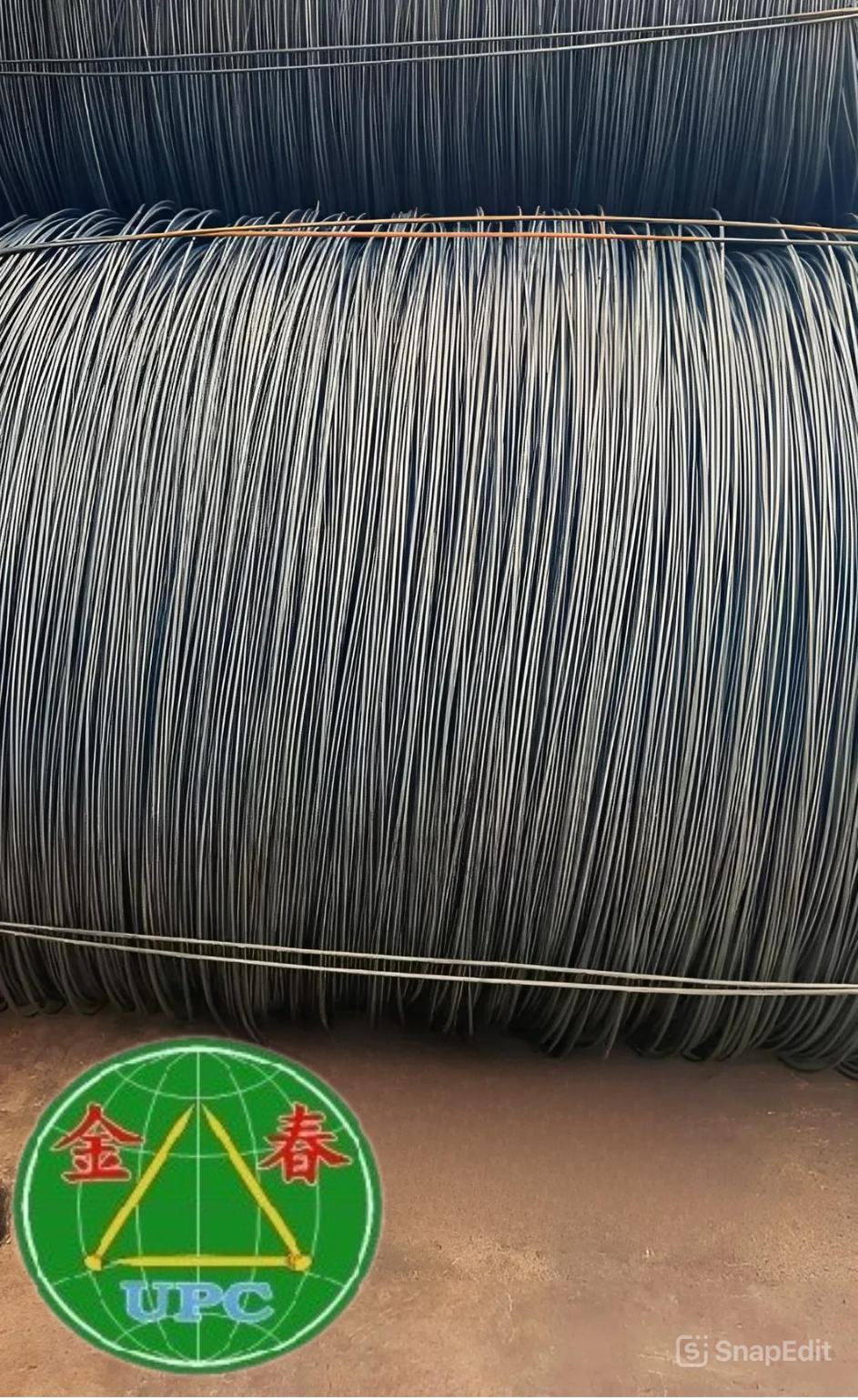
2. Wire Drawing Process
Once the raw steel is selected, the wire drawing process begins. This stage involves reducing the diameter of steel rods to create wire, the core material for loose nails. The wire drawing process is done through a series of dies, each smaller than the previous one, which gradually thins the steel to the desired thickness for the nails.
The wire drawing process must be precise to ensure consistency in the diameter of the wire, which directly affects the uniformity of the loose nails. Advanced machinery is used to perform this task, allowing manufacturers to produce large quantities of wire quickly and efficiently.
3. Nail Cutting and Shaping
Once the wire is prepared, it moves to the nail-making machine, where the wire is cut into individual pieces. Each piece will eventually become a loose nail. The wire is fed into the machine, where it is cut to the appropriate length, which determines the final length of the loose nail.
The machine then shapes the wire into nails, forming the head, shank, and point. The shank can be smooth or twisted, depending on the nail’s intended use. The head is flattened to provide a larger surface area for striking, while the point is sharpened for easier penetration into materials.
Modern machines can produce thousands of nails per minute, making this process fast and efficient. However, precision is key to ensuring that each loose nail is uniform in size, shape, and quality.
4. Heat Treatment for Hardening
After the nails are cut and shaped, they often undergo heat treatment to increase their hardness and strength. Heat treatment involves reheating the nails to a specific temperature and then rapidly cooling them, usually by quenching in water or oil. This process alters the microstructure of the steel, making the loose nails more resistant to wear and deformation.
The heat treatment process is essential for producing loose nails that can withstand heavy use in construction and other applications. The temperature, duration, and cooling method are carefully controlled to achieve the desired hardness and toughness in the final product.
5. Surface Treatment and Coating
Surface treatment and coating are critical steps in ensuring the durability and longevity of loose nails. Depending on their application, nails can be treated with various coatings to improve corrosion resistance and enhance their aesthetic appeal. Common coatings include:
- Galvanization: A zinc coating is applied to protect the nails from rust and corrosion, making them ideal for outdoor use or environments exposed to moisture.
- Phosphate Coating: This treatment provides a rough surface, enhancing the nail’s grip when used in materials like wood.
- Vinyl Coating: Vinyl-coated nails slide more easily into wood and other materials, reducing friction during installation.
- Electroplating: A thin metal coating, such as nickel or copper, can be applied to improve the appearance and corrosion resistance of the loose nails.
These coatings not only protect the nails but also enhance their performance in specific environments. The choice of coating depends on the intended use of the loose nails, with outdoor applications often requiring more robust protective layers.
6. Quality Control and Inspection
Quality control is a crucial aspect of the production process for loose nails. Manufacturers conduct rigorous inspections at various stages to ensure that the nails meet strict standards for size, shape, and performance. Common quality control measures include:
- Dimensional Checks: Ensuring that each nail meets the specified length, diameter, and head size.
- Strength Testing: Verifying that the nails can withstand the forces they will encounter during use without bending or breaking.
- Corrosion Resistance Testing: For coated nails, ensuring that the coating provides adequate protection against rust and environmental damage.
- Tensile and Shear Testing: Testing the nails’ strength to withstand pulling and shearing forces.
Manufacturers may also conduct batch testing, where a random sample of nails from each production run is inspected for defects. This ensures that the entire batch meets quality standards before being packaged and shipped to customers.
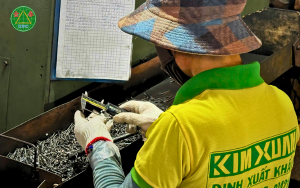
7. Packaging and Distribution
Once the loose nails pass quality inspection, they are ready for packaging and distribution. Nails are typically packed in bulk containers, boxes, or bags, depending on the quantity and customer requirements. Packaging must be secure to prevent damage during transportation and handling.
Manufacturers may offer custom packaging options, such as branded boxes or specific quantities per package, to meet the needs of different industries. Loose nails are then distributed to hardware stores, construction companies, and other buyers who rely on high-quality nails for their work.
8. Sustainability in Loose Nail Production
Sustainability is becoming increasingly important in all industries, and loose nail production is no exception. Manufacturers are adopting eco-friendly practices, such as using recycled steel, reducing energy consumption during the wire drawing and annealing processes, and minimizing waste in production.
Additionally, advancements in coating technologies are helping to reduce the environmental impact of loose nails by using less harmful chemicals in surface treatments. By prioritizing sustainability, manufacturers can produce loose nails that are not only high in quality but also environmentally responsible.
9. Innovations and Future Trends in Loose Nail Production
The loose nail industry is constantly evolving with innovations that enhance efficiency and product performance. Some of the future trends in nail production include:
- Automation and Robotics: Continued advancements in automation are improving production speed and accuracy, allowing manufacturers to produce higher volumes of nails with fewer defects.
- Smart Manufacturing: The integration of smart technologies, such as sensors and AI, is enabling real-time monitoring of the production process, leading to better quality control and optimization of resources.
- Eco-Friendly Coatings: New environmentally friendly coatings are being developed that offer improved protection against corrosion while reducing the environmental impact of traditional coatings.
zPolished finished loose nailsThese innovations will continue to drive the production of high-quality loose nails, ensuring they meet the evolving demands of the construction and manufacturing industries.